PTC ultra high pressure units have been employed in a variety of ways, but the one in the TAP pipeline remains one of the most distinctive of all.
In fact, in 2020 PTC supplied a plant used for the pipe line test of the gas pipeline which linked Italy and Albania with a submarine section.
The TAP project
The acronym TAP indicates the Trans-Adriatic Pipeline, an infrastructure for transporting natural gas by pipeline, almost 900 kilometers long, which from the Greek-Turkish border crosses Greece and Albania to arrive in Italy at Melendugno, on the Adriatic coast in the province of Lecce. It is part of the Southern Gas Corridor which transports natural gas from the Shah Deniz II field in Azerbaijan to Europe.
The pipeline is approximately 877 kilometers long, most of which in Greek territory, and includes 104 kilometers offshore in the Adriatic Sea – where it reaches a maximum depth of 820 meters – plus the last 8 kilometers in Italy, where it connects to the national gas distribution.
The pipes have a diameter of 1.22 meters in the onshore section, with a pressure of 95 bar, and 1.07 meters in the sea section, with a pressure of 145 bar, to transport approximately 10 billion cubic meters natural gas a year when fully operational and cover the needs of 7 million families. Finally, with the addition of a third compressor station, the pipeline will be able to double the quantity transported to 20 billion cubic meters per year.
PTC intervention
The pre-commissioning campaign of the 105 km of underwater pipeline between Albania and Italy was entrusted to Techfem, which requested PTC Italiana to supply an ultra-high pressure plant for pressure testing of the entire pipe line created.
Testing carried out by pumping sea water inside the pipeline, filtered and treated with ultraviolet rays, at a pressure of 188 bar, to verify on site the total integrity of the pipeline and the state compliant with the design purpose.
Pressure testing
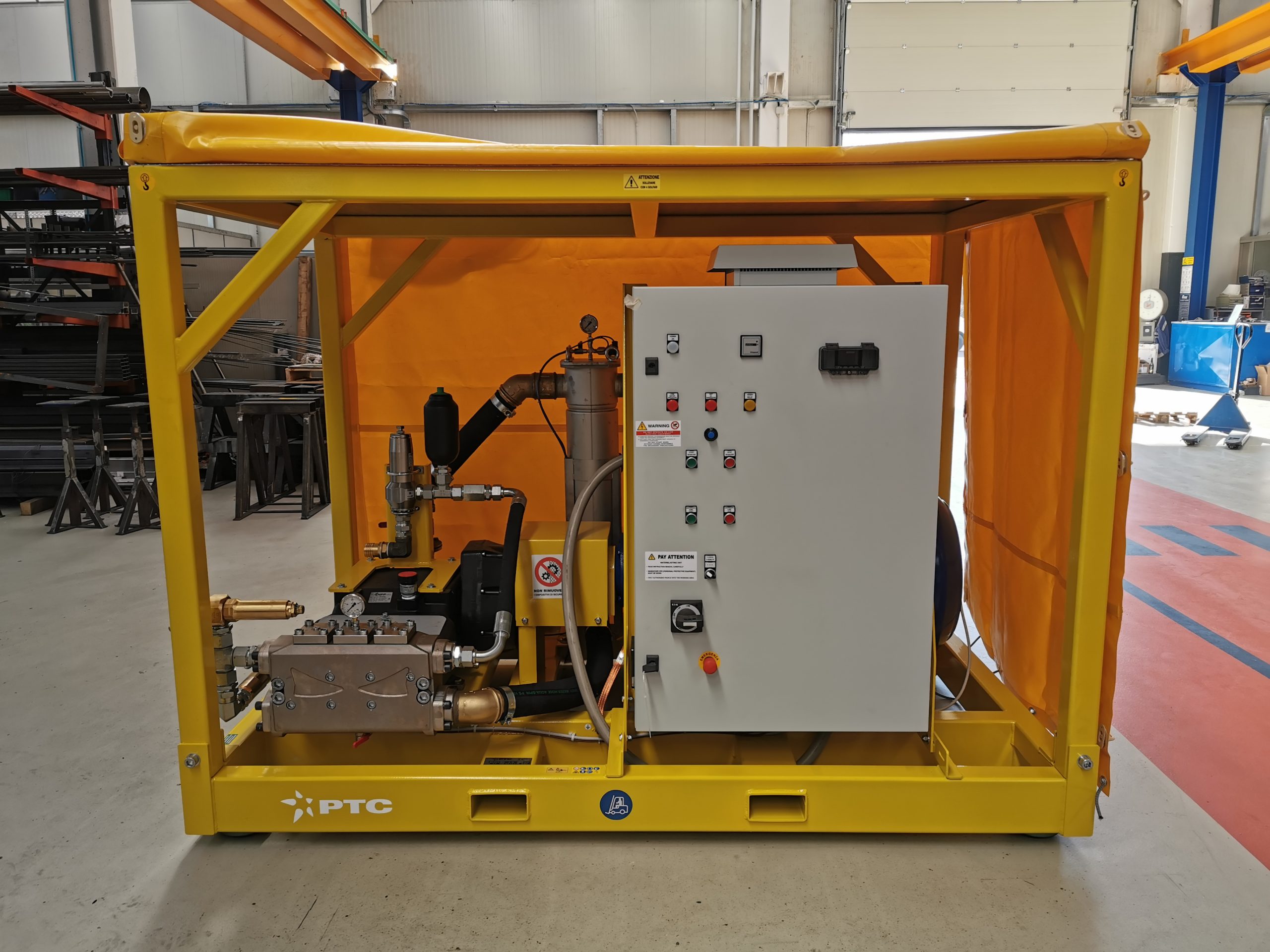
What has been done with the pressurized water is to certify the absence of leaks that could cause dangerous gas leaks. It was therefore verified that there were no pressure drops during the long hours of testing.
The ultra high pressure units were built and tested at the PTC headquarters in Rubiera, then delivered to Fano, at the Techfem headquarters which transported them to the Apulian coast, to the construction site of the consortium that built the pipeline, and directly from there they pushed the water all the way to Albania by crossing the bottom of the Adriatic Sea.
To carry out the pressure test of the pipe line created, 7 PTC 4 ultra high pressure units were therefore used, with maximum pressures of 250 bar and a flow rate of 300 liters per minute for each machine.
The 7 units were mounted in parallel, in order to multiply the flow rate up to 2100 liters per minute and be able to pressurize the pipeline over 100 kilometers long in the off-shore section, and reach the test pressure for a long period of time.
The machines, in fact, operated continuously for about 30 hours, until the necessary quantity of water was pumped into the pipeline and 188 bar was reached. Once the test was completed, the water was let out again with high pressure; the pipeline was then desalinated using fresh water and then dried to preserve it until it was released into gas.
The units for the pipe line test
Those for the pipe line test are very special high pressure units, used only for testing the pipeline, but versatile and modular to be reused for these indispensable uses.
After being used in Puglia, in fact, they were dismantled and made available for new pressure tests – albeit with different performances – already last year by Techfem for testing another pipeline in Northern Europe.