In addition to unclogging drains, purge equipment can be very useful in some industries, such as paper manufacturing.
Recently, in fact, an autonomous suction unit produced by PTC was put into operation in an important paper mill in central Italy, in Tuscany, where waste materials are recycled to produce new paper.
The production of recycled paper
In fact, for the production of recycled paper, paper mills recover boxes, packaging cardboard and other waste paper to regenerate them and give shape to new paper materials. Everything starts from the raw material: the so-called waste paper.
Waste paper comes from city collection and from industrial processing waste, selected and cleaned by specialized companies which then transform waste into secondary raw material. Arrived at the paper mill, the waste paper is introduced into a huge tank and closed there to be subjected to the pulping phase: the paper is then left to macerate in water and continuously agitated through a mechanical system, until a mixture is formed composed of 70% paper and 30% water.
After pulping, the mixture is transferred to a second tank and from there conveyed through a filtering system, then again diluted into a semi-liquid paste and spread in layers of paper of various thickness which, once dried, cut and pressed, will compose sheets and boxes.
The need for sewer cleaning
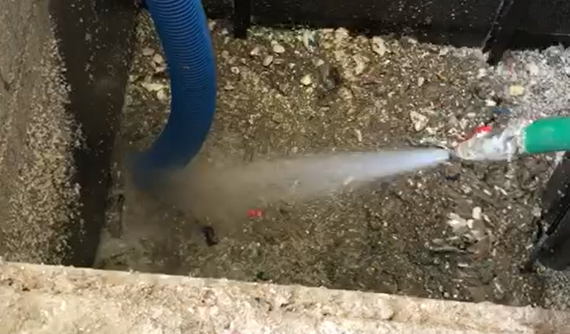
The stage affected by the sewer cleaning equipment is that of pulping, where all the recovered materials are literally pulped by introducing them into a tank full of water, where they are treated with special equipment which reduces everything into a very thick paste.
Once formed, the mixture must be transferred to a second tank for finer processing, but the high density of the compound makes it difficult to completely empty the tank, causing loss of material and time-work.
If performed manually, this phase involves the use of many workers who, using shovels and other containers, must transfer kilos and kilos of material from the tank to the cistern placed, moreover, at a height of 5 meters. Therefore, it is easy to consider the human effort and time required to complete the process.
The alternative adopted by the paper mill is to frequently contact an external company specialized in sewer cleaning, treating the pulping tank as a tank to be cleaned, emptying the aspirated paper mixture into the tank for finishing. With consequent considerable expenses for external intervention and repercussions on the planning of internal production.
The intervention of the Vortex PTC
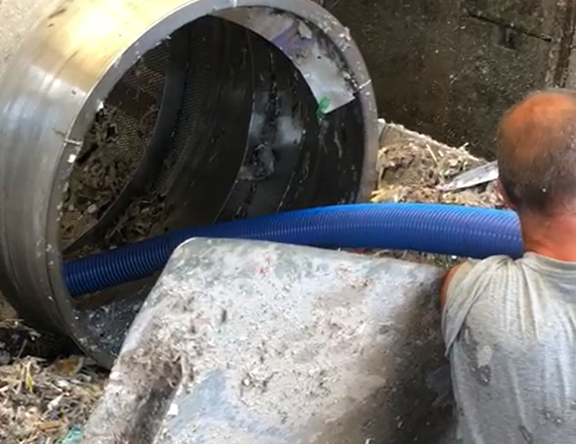
To overcome these critical issues, the company that owns the paper mill turned to PTC, a leader in the sewer equipment sector, to test the effectiveness of a Vortex suction unit in this specific process.
The PTC Vortex line is particularly suitable for the recovery and transport of non-hazardous liquids, sewage residues, sludges, semi-solids, oils and other similar materials. Vortex purge equipment is equipped with resistant steel tanks of various sizes and, depending on the needs, can be handled with forks or lifting hooks.
For the related paper mill, the Vortex Combi 1000 was used, a combined suction unit equipped with a high pressure washing system which, thanks to a 500 liter tank and a manual HP hose reel with 50 meters of hose, is capable of performing the dual function of priming liquid residues and washing with a high pressure jet. Double work with a single machine: and now we will find out why.
The test consisted of transferring 2 cubic meters of material left at the bottom of the pulping tank to the tank for finishing 5 meters higher up. First of all, having dried out particularly well, the material was wetted with the water contained in the Vortex Combi. Subsequently, with an 80 mm diameter PVC suction pipe, equipped with a steel tip and immersed at a depth of about 2 meters, the material was sucked up in just 5 minutes and emptied into the destination tank in another 5 minutes.
An operation that proved extremely easy for the powerful vacuum pumps mounted on the Vortex, sized for 3 times the capacity of the 1600 liter tank: by inverting the suction phase, the pressure pushed all the material primed into the tank quickly and with extreme power and speed. tank above, despite the high density of the pumped material.
All with the sole use of an operator on the suction tank, one on the destination tank and one to operate the machine.
Customer satisfaction
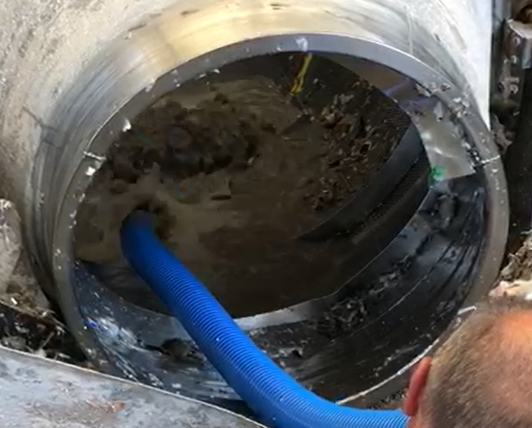
The company was very satisfied with the test, as it required electrically operated equipment, to avoid exhaust fumes and noise inside the plant.
The result, in fact, led to the purchase of reliable bleeding equipment, made entirely of stainless steel, with very powerful pumps and capable of completing the job in a very short time.
Finally, among the main recognized advantages, the possibility of moving the entire system with a simple forklift, to make it operational in other points of the plant, store it without problems or encumbrance and, if necessary, transport it with a small van.
With this choice, the paper mill was finally able to become independent of the costly and demanding external interventions of a vacuum truck, which interrupted production by cluttering up the factory with large trucks and annoying pipes.